

Comparison between Market Available
Flame Retardant Technologies
Among so many fire protection technologies available in the industry, which one is truly the most needed and offers the highest cost-performance value for modern consumers?
​​
Below are the main flame-retardant technologies currently available in the market:
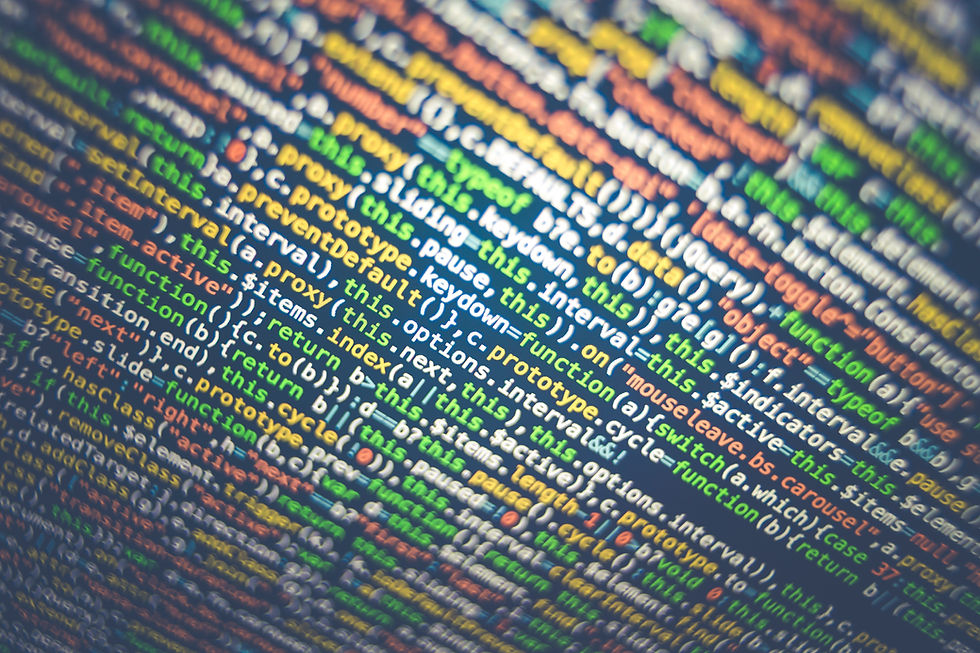
1
Expandable Fire Retardant Additives
2
Flame Retardant Plastics
Some companies produce polymers that inherently possess fire-resistant properties, eliminating the need for additional additives. For example, polyphenylene sulfide (PPS) and polyimide are flame-retardant materials used in electrical components and aerospace applications, as their chemical structure provides strong high-temperature resistance.
3
Thermoplastic Resin Systems
Certain manufacturers offer custom fire-retardant thermoplastic resins, which can be processed into specific components. For instance, fire-retardant thermoplastics such as polycarbonate (PC) and polyamide (PA), available from companies like BASF and Lanxess, can have enhanced fire resistance through the addition of specific additives.
4
Fire Retardant Coatings
In addition to relying on the inherent properties of plastics, some industries use fire retardant coatings that are applied to the surface of materials to increase their fire resistance. This method is widely used in sectors like construction and transportation to enhance fire protection without altering the core material.
Features Comparison
.jpg)
Comparing to these alternatives, Akusta's unique advantages lie in the combination of its thermoplastic flexibility, chemical water vapor release, and sound insulation properties. These three features work together to provide a more comprehensive fire and heat insulation solution.
​
Below is a comparison between Akusta and four alternative fire protection technologies (expandable additives, inherent flame-retardant polymers, thermoplastic resin systems, and fire-retardant coatings) analyzed from the perspectives of environmental impact, production complexity, and cost:
-
(1) Steam-Releasing Flame Retardant Resin Material (Akusta)
​Environmental Impact
Akusta's thermoplastic design emphasizes durability, with its fire protection performance relying on the chemical release of water vapor to absorb heat. The material itself is recyclable (depending on the formulation). The environmental impact mainly depends on the source of raw materials and the final disposal method. Due to its thermoplastic nature, it is more recyclable than thermosetting plastics, helping reduce long-term waste.
Production Complexity
Akusta is produced using standard thermoplastic processing techniques such as injection molding and thermoforming, which are well-established in the plastics industry. Therefore, this material is relatively feasible for mass production, though it requires experienced professionals with specialized expertise to handle the molding process properly.
​
Cost
The cost of Akusta may be higher than conventional plastics due to its special flame retardant and soundproof properties, but it is lower than some other high-performance materials (such as those made from high-performance polymers). The cost also varies depending on production scale and customization requirements.

-
(2) Expandable Fire Retardant Additives
Environmental Impact
Expandable fire retardant additives typically contain substances like ammonium polyphosphate, and their environmental impact varies depending on the chemical composition. While these materials are generally safe, their production and disposal processes can pose certain environmental challenges.
Production Complexity
Expandable fire retardant additives are relatively straightforward to integrate into existing plastic production processes, typically mixed with the substrate. This means no major overhaul of existing production methods is required, making it suitable for enhancing fire resistance with an efficient production process and cost-effective results.
​
Cost
The cost of adding expandable fire retardant additives is usually lower than developing entirely new fire-resistant materials (such as Akusta). However, the cost can vary depending on the concentration and quality of the additives used.

-
(3) Intrinsic Fire Retardant Polymers
Environmental Impact
Polymers such as Polyphenylene Sulfide (PPS) and Polyimide (PI) are designed with inherent fire-resistant properties, but their production processes are typically more energy-intensive compared to other materials. Additionally, due to their high-performance characteristics, these materials are often more challenging to recycle, resulting in a less favorable environmental impact.
Production Complexity
The manufacturing process for intrinsic fire retardant polymers is more complex, often requiring specialized equipment and specific conditions, making it difficult and costly to produce.
​
Cost
Intrinsic fire retardant polymers are generally more expensive than traditional plastics or materials enhanced with additives due to the need for a complex production process and high-performance raw materials.

-
(4) Thermoplastic Resin Systems
Environmental Impact
Like Akusta, thermoplastic resin systems are generally more environmentally friendly compared to thermoset polymers, as they are recyclable. However, the additives used to enhance fire resistance may have some environmental impact, depending on the chemical composition of the additives.
Production Complexity
The processing of thermoplastic resins is relatively simple, similar to Akusta, allowing them to be molded into various shapes and applied across a wide range of industries.
Cost
The cost of thermoplastic resins is typically lower than that of intrinsic fire-retardant polymers, but may be higher than that of standard thermoplastics. The addition of fire-retardant additives can increase the overall cost.
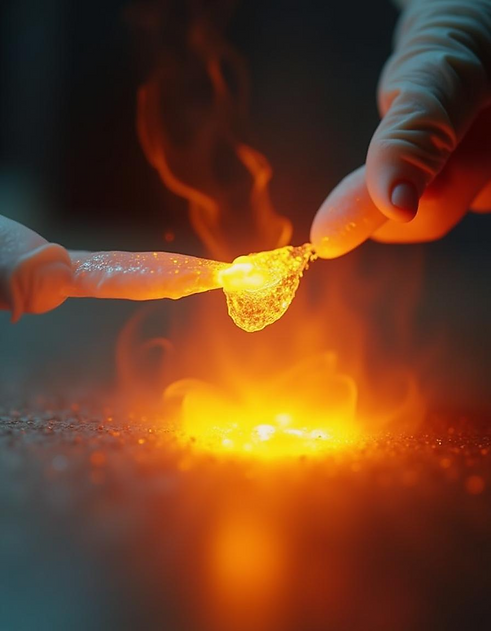
-
(5) Fire Retardant Coatings
Environmental Impact
The environmental impact of fire retardant coatings varies depending on their ingredients. Some coatings may contain harmful solvents or metals, which, if not handled properly, could cause environmental pollution.
Production Complexity
The application of fire retardant coatings is relatively simple, as it does not require altering the substrate. However, coatings can wear over time, reducing their effectiveness, meaning they must be reapplied regularly, which could increase maintenance complexity.
Cost
Fire retardant coatings are typically a cost-effective solution to enhance fire resistance, as they are applied directly to existing materials without needing to reformulate the substrate. However, the long-term costs can increase due to the need for regular reapplication.
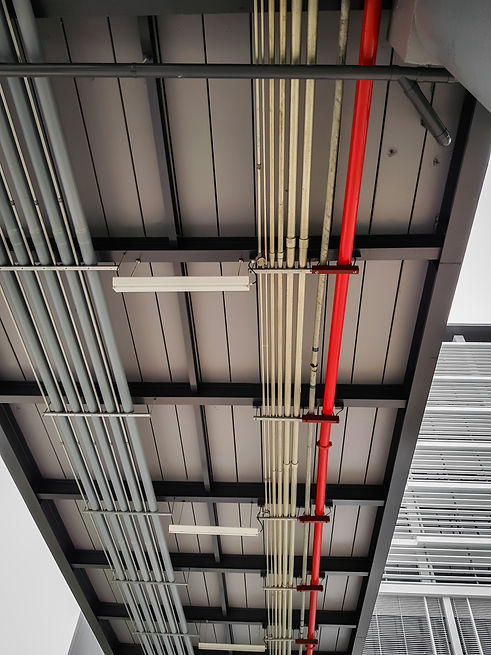
Summary
​​
Environmental Impact
Compared to thermoplastic resin systems and expandable fire retardant additives, Akusta offers better environmental performance, as it is recyclable. In contrast, inherent fire-retardant polymers and certain fire retardant coatings may have a greater environmental impact during production or disposal.
Production Complexity
Akusta and thermoplastic resin systems are relatively feasible to produce, utilizing established manufacturing processes. In comparison, inherent fire-retardant polymers and coatings require more complex processes or coating applications.
Cost
Expandable fire retardant additives are the most cost-effective option, followed by thermoplastic resin systems and Akusta. Inherent fire-retardant polymers are more expensive, while fire retardant coatings have lower initial costs but higher long-term reapplication and maintenance expenses.
Overall, Akusta offers a well-balanced solution in terms of production simplicity, environmental impact, and cost, especially when compared to inherent fire-retardant polymers, offering more competitive pricing.